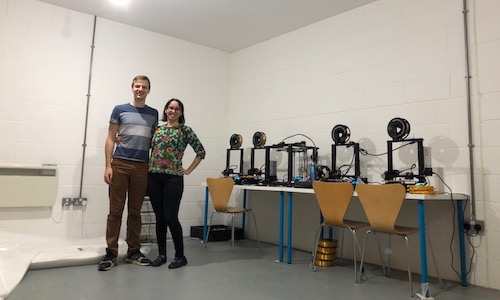
3D printing to help the NHS
As passionate software engineers, we believe the best part in our job is to solve problems and help people.
Being quite geeky, we had got ourselves a 3D printer last year and had a lot of fun with it! On our quest to make ourselves useful during the covid-19 crisis, we found a post on a 3D printing forum about people printing face shields to help healthcare workers. That’s when it all clicked, we already had most of the equipment, it just made sense for us to get started and try to help!
First steps & iterations
We first distributed a few dozen to nurses and doctors to start collecting feedback. While we were trying to find an adequate design, we quickly realised the demand for protection was much higher than we thought. More and more people would reach out and ask us how many we could make for them. We felt we needed to do more, so we started using our printer 24/7. We spent days learning more about 3D printing to tweak our configuration and other settings to optimize our prints.
Optimisation
Initially, it took us almost an hour to print a single headband. After lots of trial and error, we got this time down to 25min! That’s when we stumbled upon another issue: printing one headband faster also meant we had to constantly check on the printer to remove the headband already done and restart it. For days we used a timer to remind us to change and restart the print every 25min. It was eating up our whole day. This was not sustainable.
Scaling
We worked on a way to stack our headbands so we didn’t have to check on the print as often, which also presented new challenges. Our printer was quite cheap and temperamental. The higher the print, the higher the risk of something going wrong. After days of failed, crooked and uneven stacks, we finally nailed down the process and felt confident enough to let the printer run all night without supervision.
With these optimisations, we were suddenly able to produce a lot more face shields and started to deliver them with our bicycles every day. We started getting so much demand, we felt like we needed to do more, but our printer was already running day and night.
Getting funding
We set up a GoFundMe page to raise money so we could scale our operation. But before we could even think about buying any printers, we needed to find a space as our flat wasn’t big enough. We started to get in touch with as many people as we could to find a place. The Craft Central , which provides workspace to artists, makers and small businesses at The Forge, immediately replied and gave us a space free of charge.
Anne-Sophie Cavil , the person in charge of their communication, helped us with all our communications. She supervised our social media posts, public writings and has been of fantastic support. She also published an article about the project on their website.
Thanks to them, things really took-off.
We woke up the next morning and the fundraising exploded. We were blown away by how generous so many strangers were! Within a week, we ended up with four extra printers in our new mini factory. With our increased production, preparing all the face shields became extremely time consuming. We first need to pull apart each headband from the stack. Then we need to remove all the extra bits of plastic that are stuck on the headband and sometimes file it so it is nice and smooth. Finally, you need to punch holes in the binding covers so they can be attached on the headband. They are now ready to be delivered to hospitals by bicycle.
Building a system
The workload was manageable when we only had one printer running. It became quite problematic with 5 printers running day and night. Soon we found ourselves with stacks and stacks of headbands to prepare. On top of that, because we got the cheapest printers we could find, there would always be some maintenance or quick fix to do on at least one printer every day.
What started in our bedroom as a little project had become a full business operation. We set up a camera to monitor the printers from home and rapidly react to failures. Everyday, the output of the printers would be collected, prepared and distributed.
We were working up to 12 hours a day on this project. We were still living off our own savings and soon we would have to go back to work. We needed more help. And more help we found!
When we thought we would have to slow down due to our lack of resources, the Limehouse Community Forum heard about us online and offered to help. They provided everything we needed to expand our project: networking, extra funding and trusted volunteers. They put together a brilliant end to end system and allocated a space to prepare the headbands while respecting social distancing.
Bikeworks, a East London based cycling social enterprise, started to make the deliveries. They are picking up the stacks of headbands that we print at the Craft Central to send them to Limehouse to be prepared by the volunteers. They also help with the deliveries to hospitals and care homes.
We were able to reach out and help more and more people, even shipping to Italy and France. After a while, the demand for PPE started to slow down, as the supply chain was slowly catching up, which was great news! In the end, we produced 2,500+ PPE which is quite amazing. As the demand slowed down, we decided to stop buying more supplies. Once all the filament we currently have is used up, we will stop the operation and donate the printers to local schools.
A stellar team
This project would not have been possible without the Craft Central, the Limehouse Community Forum , Bikeworks and the astonishing contributions from the community.
We met extraordinary people with big hearts and beautiful souls. We received an overwhelming amount of support and we are so grateful for it! We are so happy we were able to help so many people and this whole project has been a fabulous adventure. It really warmed our hearts and reminded us that even in a very dire situation, there are always good people who will step up to work together and make things better.
To everyone – volunteers, donators, supporters – who contributed to this project, from the bottom of our hearts, thank you!
It is now time for us to go back to our initial project of building web and mobile applications, Specian .
If you would like to see more pictures of the project, click here . You can also watch our introduction video .
No profit has been made. All PPE have been donated.
Contributors
A special thank you to everyone who donated their time, resources and energy to make this project happen:
3DVerkstan designed this excellent visor we printed. A true masterpiece.
Craft Central offered a great (and big!) space with electricity, all free of charge. It is an unusual and very authentic place that we highly recommend. Thank you to Laurent Defontenay who introduced us to them.
Limehouse Community Forum provided a phenomenal help with logistics and funding. We definitely hope to work again with this fantastic team.
Jim Blakemore from Bikeworks fully took over all our deliveries with his remarkable service.
Media Crews edited our introduction video which yielded excellent results on social media.
Anne-Sophie Cavil guided and reviewed us with all our communications with her outstanding experience with social media and public relations. A real pleasure to work with.
Eleanor Hall assessed needs across care homes and food banks while organising and planning distribution.
Tia Shek gave hours of her time to the assembly and inventory of the face shields.
Andy Hooper scraped his fingers to the bone to sand and prepare the headbands.
Norman Ludzinski came up with some truly ingenious ways to tweak the 3D printers.